
Graepel Italiana SpA |
Perforated sheets - Technical features
Shape of holes
The most simple shapes are: round, square and triangular (equilateral).
While the triangular hole is rarely used for specific purposes, round
and square holes are indubitably the most requested types. Slot holes
and rectangular holes (sharp edges) derive from
round and square holes.
 |
 |
 |
 |
round hole |
square hole |
slot hole |
rectangular hole |
Besides these shapes, many others are available:
 |
 |
 |
 |
 |
 |
hexagonal hole |
square hole with rounded edges |
diamond-shaped hole |
triangular hole |
star-shaped hole |
key-shaped hole |
The latters find their major use for specific purposes, while the ones
on the top of the page coincide with more than 80% of the overall
production, and are used in several fields.
The perimeter of the hole is not always required to be on the same
level of the surface of the metal plate. Sometimes the whole contour
of the hole is deformed upwards or downwards (countersunk or indented
hole).
While usually the holes on a metal sheet are deformed in the same
direction, Graepel developed a system to combine the two directions of the
deformings on unique metal sheet.
Hole measurements and dimensions
Round holes are determined by the measure of its diameter "d";
square holes are determined by the measure of the side "a".
Diameters and sides up to 120 mm are possible.
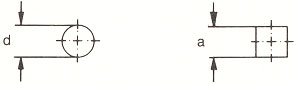 |
|
DIN 24042 regulation
allows a radius on the edge of a hole of
r max = 0,15 a |
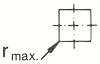 |
Slot and rectangular holes can be
determined from the measures of their width "a" and length "l".
The maximum dimension of "a" is 120 mm and "l" 200 mm
or more.
Holes obtained by punching are divided into three areas: on top the
warping area, then the cut area, and lastly the breaking point area. The
measure of the hole is obtained in the cut area.
During the standard punching of a perforated metal sheet, the section of
the holes is slightly conic in the breaking point area.
It is important that the ratio between bridge "n" and thickness of the
metal sheet do not go below 1, otherwise the space between the holes may
break.
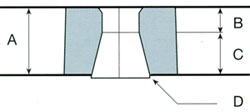 |
B = Cutting area
C = Breaking point area
E = Burr
S = Thickness |
Pitch and bar
Pitch correspond to the distance
between the centres of two contiguous holes.
Bar indicates the lesser
unperforated
area between two contiguous holes.
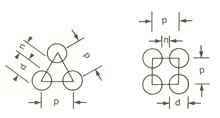 |
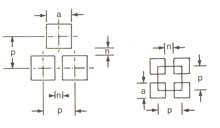 |
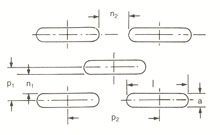 |
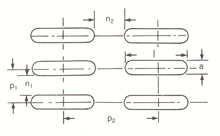 |
p = d + n
(pitch = diameter + bridge) |
p a + n
(pitch = side + bridge) |
p1 = a + n1
p2 = l + n2
n1 = p1- a
n2 = p2 - l |
Perforated areas: beginings and ends
Perforated areas are measured between the circumferences (outer sides)
of the holes starting from the first to the last row of holes.
Due to tooling reasons, the distance among
punches is double or triple if compared to the perforation pitch.
Therefore the complete perforation scheme can be obtained in full just after
the second or third hit. Likewise, the end of a perforated area
looks rough. This kind of
beginning of perforation is called "double" or "triple initial gap".
Thanks to the newest CNC punching presses, it is almost always possible
to remove these initial gaps, but it is fundamental to know that since
the original inquiry.
Nowadays many modern toolings take advantage of the double feeding to
minimize production timings and costs. Unfortunately
not every tooling is able to obtain regular perforation beginnings
and ends.
Customers often opt out this aesthetic requirement
in order to keep costs down.
The double or triple initial gap system works with every kind of
perforation.
Edges, unperforated areas and their measurement
One of the most important benefits of perforated metal plates is
the possibility to get edges and unperforated areas. Usually, the
two long sides of perforated metal sheets up to 4
mm thickness have small unperforated edges, while the two short
sides do not have any edges. Starting from 5 mm thickness the standards
provide for full unperforated perimetral edges.
Unperforated edges can be removed thanks to shear cutting. It is
also possible to allow unperforated areas in different positions,
and especially with sectional presses it is
possible to satisfy almost every request about shape and position of
unperforated areas.
Edges must be measured starting from their limit on the outer side of
the metal sheet, and not starting from the centre of the hole.
Cutting and shearing burr
Just as in any other shearing system, perforation involves the formation
of burr on the exit side of the punch. The amount of burr depends on
various factors (type of material, tool grinding, clearance between
punch and matrix, etc.). You must always consider
that on the whole
perimeter of the metal sheet cutting burrs (made during shearing)
are present. These burrs are often facing opposite
each other and the perforation burr.
Important: unless otherwise agreed, the entering side of
punches is shown on technical drawings.
Open area
The ratio between empty and full spaces, which is easy to determine
thanks to the after-written formulas, is expressed
as the percentage of the total perforated surface, threrefore it does
not consider edges and unperforated areas.
Flattening of perforated metal sheets
Perforation causes tensions to the metal plate,
deforming it; then it is necessary to flatten it with suitable
muli-cylindrical flattening machines.
For large metal sheets, wide unperforated surfaces, broad/irregular
edges, materials which are very hard or with "difficult"
perforated areas, tension may be so strong to
impair the flattening process.
Metal coils perforated then wrapped do not undergo any flattening,
therefore flatness can not be guaranteed.
Enquiries and orders
When placing enquiries or orders, the following data must be sent:
- quantity of sheets - quality of the raw material - thickness,
width and lenght of the metal sheets - measurements of the hole (placement,
parallelism for slot and rectangular holes)
- pitch (if not indicated, the normal pitch will be used)
- edges and/or unperforated areas -
requested delivery terms
When in doubt, please send a technical drawing, a
sketch or a sample, if available. |
Graepel Italiana S.p.A
46018 SABBIONETA (MN) - Via Fondi, 13 - ITALY - Tel. +39 0375 220101
- Fax +39 0375 220262
R.I. MN / C.F. / P.IVA 00500630207 - REA 135337 - Cod. Mecc.
MN005636 - Cap. Soc 516.450 i.v. -
info@graepel.it |
|